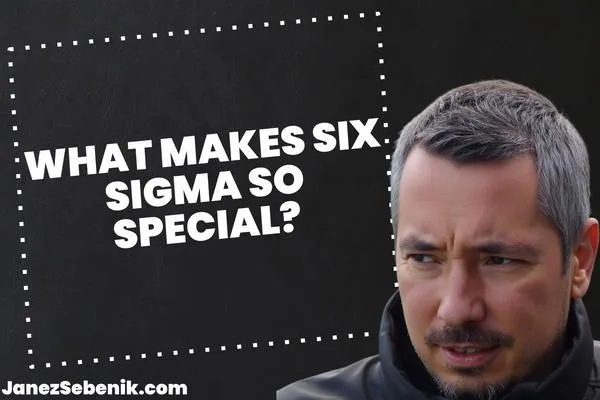
Why is it called Six Sigma?
Ever wonder why a business method has such a weird name? Six Sigma sounds like something out of a sci-fi movie. But it's actually rooted in statistics.
Six Sigma is named after the statistical concept of standard deviation, represented by the Greek letter sigma (σ). It's all about reducing defects and making processes super efficient.
The "six" part? That's the gold standard. It means a process is so good, it only has 3.4 defects per million opportunities. Pretty impressive, right? This approach has changed how many businesses operate, aiming for near-perfection in everything they do.
Key Takeaways
Six Sigma uses statistics to improve business processes
The name comes from the goal of achieving 3.4 defects per million opportunities
It's a widely used method for boosting efficiency and quality in various industries
The History of Six Sigma
Six Sigma has a rich history of improving business processes. It started with one company's quest for quality and spread worldwide. Let's dive into how it all began.
Motorola's Brainchild
In 1986, Motorola introduced Six Sigma to boost their manufacturing quality. They were facing tough competition and needed a way to up their game.
You might wonder, "What made Six Sigma special?" Well, it focused on reducing defects to near-zero levels. That's pretty ambitious, right?
Motorola didn't keep Six Sigma to themselves. They trademarked it in the early 1990s, but shared the method with other companies. Talk about generous!
Bill Smith and Mikel Harry's Influence
Bill Smith, an engineer at Motorola, came up with Six Sigma. He's like the dad of Six Sigma. But he didn't work alone.
Mikel Harry, another Motorola engineer, helped develop the method too. They were quite the dynamic duo!
These guys didn't just create a method. They started a revolution in quality control. Their work laid the foundation for what Six Sigma is today.
Think about it. Two engineers changed how businesses around the world operate. Pretty cool, huh?
Jack Welch and General Electric
In 1995, Jack Welch, the CEO of General Electric (GE), discovered Six Sigma. He fell in love with it. Can you blame him?
Welch made Six Sigma central to GE's strategy. He saw its potential to transform the company.
Under Welch's leadership, GE saved billions using Six Sigma. That's billion with a 'B'. Impressive, right?
GE's success with Six Sigma caught everyone's attention. Soon, two-thirds of Fortune 500 companies jumped on the bandwagon.
You could say Welch and GE were like Six Sigma's hype men. They showed the world what it could do.
Six Sigma: More Than a Name
Six Sigma isn't just a fancy name. It's a powerful method that can transform your business. Let's break it down so you can see why it's such a big deal.
Understanding 'Sigma'
Ever heard of standard deviation? That's what sigma means in stats. It's like a ruler for measuring how spread out your data is.
In business, you want your processes to be consistent. Sigma helps you measure that consistency.
Think of it like this: You're making pizzas. Sigma tells you how often your pizzas come out perfect versus burnt or undercooked.
The lower your sigma, the more burnt pizzas you're serving up. Not good for business, right?
The Power of the Number Six
So why six? Because it's the magic number for near-perfection.
When you hit Six Sigma, you're only messing up 3.4 times out of a million. That's insanely good!
Imagine if airlines operated at just three sigma. We'd have multiple crashes every day. Yikes!
Six Sigma pushes you to be the best. It's not about being good enough. It's about being nearly flawless.
And here's the kicker: When you aim for Six Sigma, even if you fall short, you're still way ahead of the competition.
Core Elements of Six Sigma
Six Sigma isn't just a fancy name. It's a powerful system with specific parts that work together. Let's break it down so you can see how it all fits.
DMAIC: The Six Sigma Roadmap
DMAIC is your GPS for problem-solving. It stands for Define, Measure, Analyze, Improve, and Control. Think of it as your step-by-step guide to fixing stuff.
First, you define what's wrong. Then you measure how bad it is. Next, you analyze why it's happening. After that, you improve things. Finally, you make sure it stays fixed.
It's like fixing a leaky faucet. You spot the drip, see how much water you're wasting, figure out why it's leaking, replace the washer, and then check it's not dripping anymore.
Tools of the Trade
Six Sigma's toolbox is packed with cool gadgets. You've got statistical tools to crunch numbers and spot patterns.
There's also process mapping to see how things flow. And don't forget about root cause analysis - it's like being a detective for problems.
You'll use surveys to gather info and control charts to keep an eye on things. It's like having a Swiss Army knife for business problems.
These tools help you dig deep and find real solutions. No more guessing or quick fixes that don't last.
Roles and Belt Rankings
In Six Sigma, you're not just an employee - you're a ninja warrior. There are different belt levels, just like in martial arts.
White Belts: The newbies. They know the basics.
Yellow Belts: They can help out on projects.
Green Belts: These folks lead small projects.
Black Belts: The project masters. They're in charge of big changes.
Master Black Belts: The sensei of Six Sigma. They train others and oversee everything.
Each level has its own skills and responsibilities. It's like leveling up in a video game, but for your career. The higher you go, the more impact you can make.
Six Sigma in Practice
Six Sigma isn't just theory. It's a game-changer in real-world business. Companies use it to crush defects, boost quality, and make customers happy.
From Defects to Success
You know that feeling when something breaks right after you buy it? That's a defect. Six Sigma hates defects. It's all about making stuff that doesn't break.
In manufacturing, Six Sigma is like a superhero. It swoops in and saves the day by cutting down mistakes. How? By measuring everything and fixing problems before they happen.
Think about your phone. It works because some company used Six Sigma to make sure it's not a dud. Pretty cool, right?
Lean Six Sigma Connection
Lean Six Sigma is like Six Sigma's cooler cousin. It takes all the good stuff from Six Sigma and adds a twist: cutting out waste.
You know when you're waiting forever for your food at a restaurant? That's waste. Lean Six Sigma would fix that. It makes things faster and cheaper without messing up quality.
Companies love this combo. It's like getting a two-for-one deal on making their business awesome.
Success Stories in Business
Want to know who's crushing it with Six Sigma? Let's talk big names.
Amazon uses it to get your packages to you fast. They're obsessed with making customers happy, and Six Sigma helps them do it.
Fortune 500 companies? Yeah, they're in on it too. General Electric saved billions (that's with a B) using Six Sigma.
Even hospitals use it. They cut down on mistakes and save lives. That's pretty epic.
Six Sigma isn't just for huge companies. Small businesses use it too. It's like a secret weapon for operational excellence.
Impact on Business and Culture
Six Sigma has shaken up how companies operate. It's changed the game in quality control, given businesses an edge, and transformed how work gets done.
Quality Management Revolution
Six Sigma brought a new approach to quality. It's all about cutting down errors big time.
You know those annoying defects in products? Six Sigma aims to make them super rare. We're talking 3.4 defects per million chances. That's crazy good!
Companies started measuring everything. Data became king. No more guessing games - now it's all about cold, hard facts.
This shift made customers happier. They got better products and services. And businesses? They saved a ton of money by avoiding costly mistakes.
Competitive Advantage Unleashed
Six Sigma isn't just about making stuff better. It's about crushing the competition.
You implement Six Sigma, and suddenly you're way ahead of the pack. Your products are top-notch. Your processes are smooth as butter.
Customers notice. They start picking you over others. Why? Because you're delivering the goods, consistently.
It's not just big corporations either. Small businesses jumped on board too. They saw how Six Sigma could help them punch above their weight.
And here's the kicker - it works across industries. Manufacturing, healthcare, finance - you name it, Six Sigma can boost it.
Transforming Organizational Processes
Six Sigma isn't just a tool. It's a whole new way of thinking about work.
You start looking at every process in your company. What's working? What's not? You become obsessed with efficiency.
Employees get trained in Six Sigma methods. They become problem-solving ninjas. Everyone from the CEO to the front-line staff gets involved.
It changes company culture. Continuous improvement becomes the norm. You're always looking for ways to do things better, faster, cheaper.
And it's not just about cutting costs. It's about creating value. For your customers, your employees, and your bottom line.
Getting Six Sigma Certified
Getting Six Sigma certified can boost your career and help you make better business decisions. It's like leveling up in a video game, but for your job skills.
The Certification Journey
Ready to start your Six Sigma adventure? First, pick a certification level. You've got options from Yellow Belt to Master Black Belt. Each level needs different training and exams.
American Society for Quality offers popular certifications. But they're not the only game in town. Many companies and schools have their own programs.
You'll need to study hard and practice using Six Sigma tools. Expect to spend weeks or months preparing, depending on the level you choose.
Most certifications require passing an exam. Some also need real-world project experience. Don't worry, you've got this!
The Belts and What They Mean
In Six Sigma, belts aren't just for holding up your pants. They show your skill level:
Yellow Belt: You know the basics. Great for team members.
Green Belt: You can lead small projects and help Black Belts.
Black Belt: You're the project leader and Six Sigma expert.
Master Black Belt: You're the Six Sigma sensei, training others and tackling big problems.
Each belt means more knowledge and responsibility. Yellow and Green Belts often work on Six Sigma part-time. Black Belts and above? It's usually their full-time gig.
Higher belts can mean better pay and more job options. But remember, it's not just about the title. It's about using what you learn to crush it at work.
Six Sigma Today and Beyond
Six Sigma keeps evolving. It's not just for manufacturing anymore. Now it's used in tech, healthcare, and even government. The future looks bright for this problem-solving powerhouse.
Adaptation in the Age of Tech
You might think Six Sigma is old school. Think again. It's getting a tech makeover. Data analytics is breathing new life into it.
Artificial intelligence is joining the party too. It's like Six Sigma on steroids. You can spot patterns faster than ever before.
Companies are using AI to predict defects before they happen. It's like having a crystal ball for quality control. Pretty cool, right?
Tech isn't replacing Six Sigma. It's supercharging it. You're getting the best of both worlds.
Continuous Improvement and Future Visions
Six Sigma isn't sitting still. It's always looking for ways to get better. That's what continuous improvement is all about.
You're not just fixing problems. You're preventing them. It's like playing chess while everyone else is playing checkers.
The future of Six Sigma? It's all about efficiency. You'll be doing more with less. Waste? That's so last century.
Imagine a world where every process is streamlined. Where defects are rare as unicorns. That's the Six Sigma vision. And you're part of making it happen.