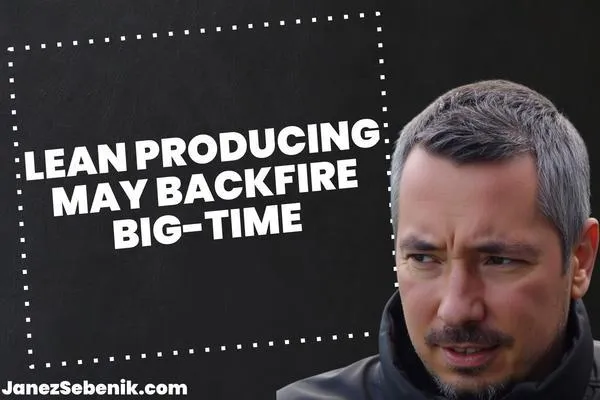
What are the disadvantages of lean production?
Lean production sounds awesome, right? Less waste, more efficiency. But hold up. It's not all sunshine and rainbows.
Lean manufacturing can create new problems while solving others. It's like trying to fix a leaky roof and accidentally flooding your basement.
You might think lean is the answer to all your production woes. But before you jump in, let's take a look at some of the downsides. Trust me, you'll want to know these before you go all-in on lean.
Key Takeaways
Lean can disrupt your productivity in the short term as you overhaul processes.
Your employees might resist the changes required by lean manufacturing.
Lean techniques can create new inefficiencies if overused or poorly implemented.
Core Concepts of Lean Production
Lean production aims to maximize value while minimizing waste. It's all about doing more with less and keeping things simple.
Lean Manufacturing Origins
Lean manufacturing started in Japan after World War II. Toyota was the pioneer. They created the Toyota Production System, which became the foundation of lean.
The goal? Make cars faster and cheaper than American companies. Toyota's system focused on eliminating waste and improving efficiency.
This approach spread globally. Now, companies in all industries use lean principles to boost productivity and cut costs.
Elimination of Waste
Waste is your enemy in lean production. It's anything that doesn't add value for the customer.
There are 8 types of waste to watch out for:
Overproduction
Waiting
Transportation
Over-processing
Inventory
Motion
Defects
Unused talent
Your job is to find and eliminate these wastes. This helps you save time, money, and resources.
Minimizing waste is a key advantage of lean manufacturing. It makes your processes smoother and more efficient.
Principles of Lean
Lean production follows five main principles:
Define Value: Understand what your customer wants and is willing to pay for.
Map the Value Stream: Identify all steps in your production process. Keep the valuable ones, ditch the rest.
Create Flow: Make your processes run smoothly without interruptions or delays.
Establish Pull: Produce only what's needed, when it's needed. No more, no less.
Seek Perfection: Always strive to improve. Make continuous improvement part of your culture.
These principles guide you in creating a lean system. They help you focus on what matters most: delivering value to your customers.
Negative Aspects of Lean Strategies
Lean production isn't all sunshine and rainbows. It's got some dark clouds too. Let's take a look at what can go wrong when you push efficiency too far and forget about the people doing the work.
Overemphasis on Efficiency
You know that feeling when you're trying to squeeze every last drop out of a lemon? That's what lean manufacturing can feel like sometimes.
You're so focused on cutting waste that you might accidentally cut the good stuff too. Oops! It's like trying to trim your hair and going bald instead.
Sometimes you can get so caught up in the numbers that you forget about quality. You might save a few bucks, but your customers aren't gonna be happy with shoddy products.
And what about when things go wrong? If you've cut everything to the bone, you've got no wiggle room. One hiccup and your whole operation could grind to a halt.
Neglect of Human Factors
Remember, your workers aren't robots (at least not yet). Lean techniques can push people too hard.
You might think you're boosting productivity, but you're just stressing everyone out. Stressed workers make mistakes. And mistakes? They cost you big time.
Constant pressure to improve can burn people out. Your top performers might jump ship, leaving you high and dry.
And let's not forget about creativity. When you're always focused on efficiency, there's no room for innovation. You might save a penny today, but you're losing dollars tomorrow.
So, while lean strategies can be great, you've gotta keep an eye on the human side. Balance is key, my friend.
Operational Challenges
Lean production can trip you up if you're not careful. It's not all smooth sailing, and you need to be ready for some bumps in the road.
Continuous Improvement Demands
You gotta be on your toes with lean. It's like a never-ending marathon. Firms adopting lean can lose sight of the big picture if they're not careful.
You're always looking for ways to get better. Every. Single. Day. It's exhausting.
Your team needs to be all in. If they're not, it's like trying to push a boulder uphill.
And here's the kicker: sometimes you can overdo it. You might spend so much time tracking waste that you forget to actually make stuff.
It's a balancing act. You want to improve, but not at the cost of your sanity or productivity.
Dependency on Stable Demand
Lean production is like a finely tuned machine. It works great when everything's steady. But throw in some chaos, and it can all fall apart.
You're keeping inventory low. That's cool when demand is predictable. But what happens when it spikes?
You might not have enough stock to meet sudden increases in orders. Oops.
Your suppliers need to be on point too. If they slip up, your whole production line could screech to a halt.
And let's talk about your workforce. You've got it lean and mean. But if demand drops, you might have to let people go. Not fun.
It's a tightrope walk. You're trying to stay efficient without leaving yourself vulnerable to market swings.
Financial Implications
Lean production can hit your wallet hard at first. But it might pay off big time later. Let's dive into the money side of going lean.
Costs of Lean Transition
Switching to lean isn't cheap. You'll need to train your team. That costs money and time. New equipment? More cash out the door.
You might need to hire lean experts. They don't come cheap. And your productivity might dip during the change. That means less money coming in.
But here's the kicker: these costs are investments. They're like planting seeds. It might hurt now, but you're setting up for future growth and savings.
Impact on Cash Flow
Lean can be a cash flow game-changer. In a good way. You'll carry less inventory. That means less money tied up in stuff sitting around.
Your production will get faster. You'll turn raw materials into cash quicker. It's like speeding up your money machine.
But watch out. Lean systems can be fragile. One hiccup in your supply chain, and you might run out of stock. No stock means no sales. No sales means no cash.
The trick is balance. You want to be lean, not anorexic. Keep enough buffer to stay safe, but not so much that you're wasting money.
People and Culture
Lean production can mess with your company's people and culture. It's not all smooth sailing. You'll face some challenges when it comes to your team and how they work.
Intensive Training Needs
You gotta train your people. A lot. Lean isn't something you can just slap on and expect magic. Your team needs to learn new skills, new ways of thinking, and new processes.
It's not cheap or quick. You're looking at ongoing training sessions, workshops, and maybe even bringing in experts. That's time and money out of your pocket.
And here's the kicker: some folks might not get it. They might struggle to adapt. You could end up with a split between those who "get" lean and those who don't.
Potential Labor Resistance
Your team might push back. Hard. Lean often means changing how people have worked for years. That's scary for a lot of folks.
They might think lean means job cuts. Or that it's just another fad that'll make their lives harder. You'll need to convince them it's worth it.
Some might flat out refuse to change. You could lose good people who just can't or won't adapt. That's a real risk you've gotta consider.
And if your union's involved? Buckle up. They might see lean as a threat to job security or working conditions. You'll need to negotiate carefully.
Quality and Adaptability Issues
Lean production can be a double-edged sword. It's great for cutting costs, but it might bite you in the butt when it comes to quality and staying flexible. Let's dive into the nitty-gritty.
Risk of Quality Dip
You know how they say "you get what you pay for"? Well, that applies here too. When you're trying to minimize waste, sometimes quality takes a hit.
Think about it. You're cutting corners to save cash. But what if those corners were actually important? Oops.
Your products might not be as sturdy or reliable as before. And let's face it, nobody likes a flimsy product that breaks after two uses.
Customer complaints might start rolling in. Your reputation could take a nosedive faster than you can say "lean production".
Adaptability to Market Changes
Lean production is like a well-oiled machine. Sounds great, right? Not always.
When the market shifts, you need to be able to pivot. But with lean production, you're set up for one thing and one thing only.
Changing gears? That's gonna cost you. Time, money, resources - the whole shebang.
You might miss out on new opportunities because you're too focused on staying lean. It's like wearing blinders at a buffet.
Employee resistance can be a real pain too. People get comfy with their routines. Asking them to change? Good luck with that.
Remember, the market waits for no one. If you can't adapt, you're toast.
Lean Integration with Business Systems
Integrating lean with your business systems can be tricky. It's not all sunshine and rainbows. Let's dive into some challenges you might face.
Compatibility with ERP Systems
Your ERP system might not play nice with lean principles. It's like trying to fit a square peg in a round hole.
Most ERPs are built for traditional manufacturing. They love big batches and long lead times. Lean? Not so much.
You'll need to tweak your ERP to handle smaller batches and quicker turnarounds. It's doable, but it's gonna cost you time and money.
Some ERPs are getting smarter, though. They're starting to support lean practices. But you'll need to do your homework to find the right fit.
Lean vs. Six Sigma
You've probably heard of Six Sigma. It's lean's fancy cousin. Both want to make your business better, but they go about it differently.
Lean focuses on cutting waste. Six Sigma is all about reducing variation. They can work together, but it's not always smooth sailing.
You might find your team split between the two approaches. It's like having two cooks in the kitchen with different recipes.
The key is finding the right balance. Use lean to streamline processes. Then, bring in Six Sigma to fine-tune and reduce defects.
Remember, it's not about choosing one over the other. It's about using both to give you a competitive advantage.
Customer and Supplier Dynamics
Lean production can mess with your relationships. When you try to cut the fat, it's not all sunshine and rainbows.
Supplier Coordination Complexities
You're gonna need some ninja-level skills to handle your suppliers. Why? Because lean production demands perfect timing. You want parts to arrive just when you need 'em. No earlier, no later.
But here's the kicker: your suppliers might not be on board with your lean lifestyle. They've got their own schedules and problems. And when they mess up, guess who's left holding the bag? You are.
Supply chain hiccups can leave you high and dry. No parts means no production. And that means angry customers.
Customer Relationship Management
Speaking of customers, they can be a real pain in lean production. You're trying to eliminate waste, right? That means you're not keeping loads of extra inventory around.
But what happens when a customer suddenly wants more than usual? You're stuck between a rock and a hard place. You can't just pull extra product out of thin air.
This can lead to some awkward conversations. "Sorry, we can't meet your sudden demand." Not exactly music to a customer's ears, is it?
And if you keep disappointing them, they might just take their business elsewhere. Ouch. That's not the kind of waste elimination you were going for.
Concluding Thoughts
Lean production isn't all sunshine and rainbows. You gotta watch out for some pitfalls.
Sure, waste reduction sounds great. But if you push it too far, you might end up with new problems.
Your workers could feel the squeeze. Constant pressure to be "lean" can lead to burnout. Not cool.
Don't forget about your customers. Lean sometimes means less inventory. What if demand spikes? You could be caught with your pants down.
Cost savings are sweet, but watch out. Cutting too deep might hurt quality. Nobody wants that.
Remember, lean isn't one-size-fits-all. What works for Toyota might not work for you.
So, should you go lean? Maybe. Just keep your eyes open and your brain turned on.
Lean can be powerful when done right. But like anything worth doing, it takes work. And sometimes, it bites back.