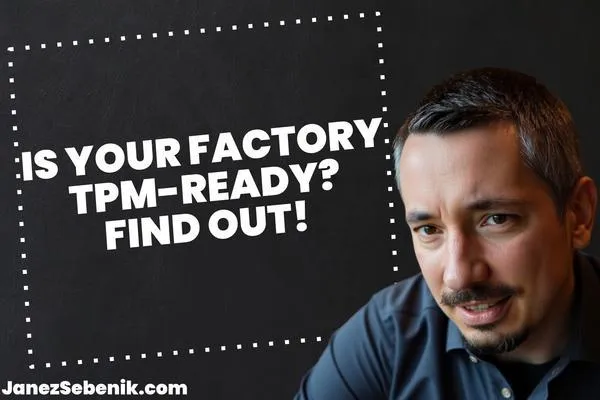
What Are the 5 Pillars of Total Productive Maintenance?
Want to boost your factory's performance? Total Productive Maintenance (TPM) is your secret weapon. It's not just about fixing machines when they break. It's about creating a culture where everyone takes care of equipment.
The five pillars of TPM are the foundation for making your operations run like a well-oiled machine. These pillars help you cut down on breakdowns, reduce defects, and pump up productivity. They're the key to turning your factory into a lean, mean, production machine.
Ready to dive in? Let's explore how these pillars can transform your workplace. You'll see why companies around the world are adopting TPM to stay ahead of the game. It's time to take your maintenance game to the next level.
Key Takeaways
TPM boosts productivity by involving everyone in equipment care
The five pillars provide a framework for reducing downtime and defects
Implementing TPM can lead to significant improvements in efficiency and quality
Understanding TPM
TPM helps you make your machines work better and last longer. It's all about keeping things running smoothly and avoiding problems before they happen.
The Core Philosophy of TPM
TPM is about teamwork. Everyone in the company plays a part in keeping the equipment running well. It's not just the maintenance team's job.
You focus on preventing breakdowns, not just fixing them when they happen. Think of it like brushing your teeth to avoid cavities.
TPM aims for perfect production. That means no breakdowns, no slowdowns, no defects, and no accidents. It's a big goal, but it's what you're shooting for.
You'll use data to make decisions. Track how well your machines are doing and use that info to improve them.
Benefits of TPM
TPM can seriously boost your productivity. When your machines run better, you make more stuff with less hassle.
You'll save money on maintenance. By fixing small issues before they become big problems, you avoid costly repairs.
Your equipment will last longer. Regular care means you won't have to replace machines as often.
Quality improves too. Well-maintained equipment produces better products with fewer defects.
Safety gets a boost. When machines are in top shape, there's less risk of accidents.
TPM helps create a culture of continuous improvement. Your team will always be looking for ways to make things better.
Five Pillars of TPM
TPM helps you keep your equipment running like a well-oiled machine. It's all about getting everyone involved and fixing problems before they happen. Let's dive into the five key pillars that make it work.
Autonomous Maintenance
This is where operators become equipment ninjas. You train them to handle basic maintenance tasks themselves. They clean, lubricate, and inspect their machines daily.
It's like teaching your kid to make their own bed. At first, it's a hassle. But soon, they're doing it without you nagging them.
Operators spot issues early, preventing bigger problems. They feel more ownership of their equipment. It's a win-win.
Plus, it frees up your maintenance pros to focus on trickier stuff. Your equipment stays in top shape, and downtime drops like a rock.
Planned Maintenance
Think of this as your equipment's regular check-up. You schedule maintenance based on data, not guesswork.
You track how often things break down. You figure out the best times to do maintenance without disrupting production.
It's like changing your car's oil before the engine seizes up. You prevent problems instead of scrambling to fix them.
This pillar uses preventive maintenance techniques to keep things running smoothly. You'll see fewer breakdowns and longer equipment life.
Quality Maintenance
This pillar is all about making sure your equipment cranks out perfect products every time. You focus on eliminating defects at the source.
You analyze your processes to find what causes quality issues. Then you fix those root causes.
It's like figuring out why your cookies always burn, then adjusting your oven temperature. You stop the problem before it starts.
This approach leads to better product quality and less waste. Your customers will love you for it.
Focused Improvement
Here's where you become a problem-solving ninja. You gather small teams to tackle specific issues.
Maybe your machine keeps jamming. You get operators, maintenance folks, and engineers together to figure out why.
It's like a brainstorming session, but with wrenches. You use data and teamwork to find creative solutions.
This pillar helps you continuously improve your equipment effectiveness. You'll see better performance and fewer losses over time.
Early Equipment Management
This pillar is all about learning from the past to build a better future. You use your maintenance know-how when buying new equipment.
You consider maintenance needs when designing or selecting new machines. It's like choosing a low-maintenance pet instead of a high-strung one.
You also focus on getting new equipment up and running quickly. You train operators and set up maintenance plans from day one.
This approach helps you avoid repeating old mistakes. Your new equipment will be more reliable and easier to maintain from the start.
TPM Implementation
Implementing Total Productive Maintenance isn't a walk in the park. But don't worry, we've got you covered. Let's break it down into bite-sized chunks that'll make your life easier.
The Road to Implementing TPM
First things first, you need a game plan. Start by picking a pilot area to test the waters. This could be a single machine or a small production line.
Next, gather your troops. Form a TPM team with members from different departments. You want a mix of operators, maintenance folks, and managers.
Now, it's time to set some goals. What do you want to achieve? Less downtime? Fewer defects? Write it down and make it measurable.
Create a timeline. Rome wasn't built in a day, and neither is a solid TPM program. Give yourself enough time to do it right.
Education and Training
Knowledge is power, my friend. And in TPM, it's the secret sauce.
Start by teaching everyone the basics of TPM. And I mean everyone - from the CEO to the janitor. They all play a part.
Train your operators to do routine maintenance tasks. Cleaning, lubricating, tightening bolts - the simple stuff that keeps machines humming.
Don't forget about your maintenance team. They need to level up their skills too. Advanced troubleshooting, predictive maintenance techniques - the works.
Use a mix of classroom sessions and hands-on training. People learn better when they get their hands dirty.
TPM in Daily Operations
Now it's time to put TPM into action. Start small and build up.
Implement autonomous maintenance. Let operators take charge of their equipment. They'll feel like superheroes.
Set up regular maintenance schedules. No more "fix it when it breaks" mentality. You're playing offense now, not defense.
Use visual management tools. Whiteboards, color-coded tags, you name it. Make it easy for everyone to see what's going on.
Hold daily TPM meetings. Keep 'em short and sweet. Review yesterday's issues and today's goals.
Remember, communication is key. Make sure everyone's on the same page. TPM only works when everyone's pulling in the same direction.
Advanced TPM Topics
TPM isn't just about fixing machines when they break. It's about keeping them running smoothly all the time. Let's dive into some advanced techniques and how to measure success.
Maintenance Techniques
You've got to stay ahead of the game. Predictive maintenance is your secret weapon. It's like having a crystal ball for your equipment.
Use sensors and data to spot issues before they become problems. It's like catching a cold before you start sneezing.
Proactive maintenance is another game-changer. You don't wait for things to go wrong. You actively look for ways to make your machines better.
Think of it as giving your equipment a spa day. Regular check-ups, cleanings, and upgrades keep everything running smoothly.
Measuring TPM Success
You can't improve what you don't measure. That's where Overall Equipment Effectiveness (OEE) comes in. It's your TPM report card.
OEE looks at three things: availability, performance, and quality. It's like checking your machine's pulse, speed, and accuracy all at once.
Availability is simple. Is your machine ready when you need it? Performance measures how fast it's running. Quality checks if it's doing the job right.
Track these numbers religiously. They'll tell you if your TPM efforts are paying off. Remember, small improvements add up. A 1% boost in OEE can mean big bucks over time.
Creating a TPM Culture
Building a strong TPM culture is all about teamwork and safety. It's not just a program, it's a way of life in your factory.
Let's dive into how you can make it happen.
Safety, Health, and Environment
Safety first, always. In TPM, it's not just a slogan - it's your top priority. You want zero accidents, period.
Start by identifying hazards in your workplace. Then, eliminate them one by one.
Train your team to spot risks before they become problems.
Create a safe working environment that protects both people and machines. It's a win-win. Happy workers are productive workers.
Don't forget about health. Encourage regular check-ups and promote wellness programs. A healthy team is a strong team.
Environmental care matters too. Reduce waste, save energy, and cut pollution. It's good for the planet and your bottom line.
Role of Management and Teams
Leadership sets the tone. As a manager, you're the TPM cheerleader. Show your commitment every day.
Empower your teams. Give them the tools and training they need. Encourage operators to take ownership of their equipment.
Communication is key. Have regular meetings to share ideas and solve problems. Make sure everyone knows the TPM goals and their role in achieving them.
Create cross-functional teams. Mix operators, maintenance staff, and engineers. They'll learn from each other and come up with amazing solutions.
Celebrate wins, big and small. Did you reduce downtime? Throw a pizza party! Hit a safety milestone? Give out some cool swag.
Creating a TPM culture takes time. Be patient, stay consistent, and watch your factory transform.
Challenges and Solutions
You're gonna face some roadblocks on your TPM journey. But don't sweat it, I've got your back.
Productivity loss is a big one. Your team might resist change at first. Solution? Get them pumped up! Show them how TPM will make their jobs easier.
Unplanned downtime can be a real pain. It's like when your car breaks down on the way to a hot date. Fix it by nailing that preventive maintenance schedule.
Production losses happen. But you can crush them. How? By training your team to spot and fix small issues before they blow up.
Quality loss is a sneaky thief. It steals your profits when you're not looking. Beat it by implementing regular equipment checks.
Here's a quick hit list to tackle these challenges:
Train your team like champions
Set clear goals and celebrate wins
Use data to make smart decisions
Keep communication flowing like a river
TPM is about continuous improvement. You'll hit bumps, but keep pushing. Your equipment will thank you, and so will your wallet.
The Future of TPM
You know what's coming? TPM is about to get wild. It's not just for factories anymore.
Think about it. Every business wants to save money and make customers happy. That's where TPM comes in.
You'll see TPM spreading to offices, hospitals, and even your local coffee shop. It's all about making things run smoother.
Here's what you can expect:
AI-powered maintenance predictions
Virtual reality training for workers
Robots doing the dangerous stuff
But don't worry, it's not all sci-fi. The basics still matter. You'll always need to keep things clean and well-oiled.
Lean production will get even leaner. You'll cut waste like never before. Your customers will love the consistent quality.
Remember, it's all about teamwork. From the CEO to the new guy, everyone's in on TPM.
So get ready. The future of TPM is bright, and you're gonna be a part of it. Keep improving, keep learning, and watch your business soar.